
Backed By:
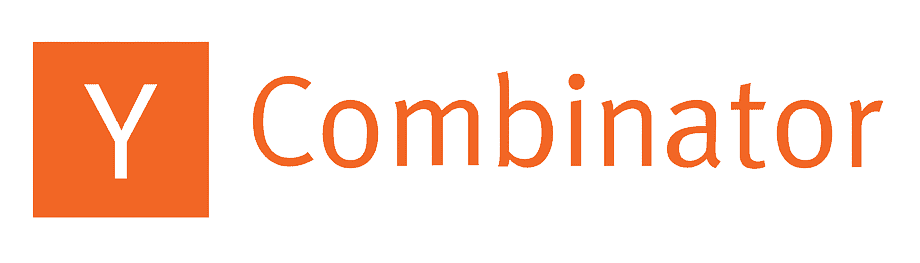
Automation solutions for service technicians. Works with all your existing solutions and CRMs.
Master HVAC inventory management with our comprehensive guide. Learn how effective stock control can reduce costs by 35%, improve first-time fix rates by 45%, and optimize your service operations.
Discover how modern inventory management practices can transform your HVAC business. From parts tracking to stock optimization, learn proven strategies to reduce costs and improve service efficiency.
Effective inventory management is crucial for HVAC service success, directly impacting your bottom line and service quality. As highlighted in our comprehensive HVAC software guide, proper stock control can reduce costs by up to 35% while improving first-time fix rates by 45%. This guide explores how modern inventory management solutions can transform your HVAC operations.
A comprehensive inventory management system, like Fieldproxy's solution, should address these key areas:
Modern inventory systems provide instant visibility into:
Intelligent reordering systems help maintain optimal stock levels by:
As detailed in our Mobile App Best Practices Guide, technicians need quick access to:
Successfully implementing inventory management requires a phased approach:
Configure your inventory management system with:
Implement these proven strategies to maximize efficiency:
Categorize parts based on value and usage:
For non-critical parts, implement JIT practices:
Optimize service vehicle inventory with these practices:
Track these essential metrics to measure inventory management success:
MetricTargetMeasurement FrequencyInventory Turnover Rate8-12 times annuallyMonthlyFirst-Time Fix Rate>90%WeeklyStock Accuracy>98%DailyCarrying Cost<15% of inventory valueQuarterly
Address typical inventory management challenges with these solutions:
Connect inventory management with other business systems for maximum efficiency:
Effective inventory management is crucial for HVAC service success. With Fieldproxy's comprehensive inventory management solution, you can optimize stock levels, reduce costs, and improve service efficiency. The key is to implement a system that provides real-time visibility, automates routine tasks, and integrates with your existing operations.
Ready to transform your inventory management? Start your free trial with Fieldproxy today and discover how our solution can optimize your HVAC parts and stock control.
Book a demo and get two months free!